- Home
- Blog
- Glass Processing
- What are the Different Types of Glass Processing and Glass Finishing?
What are the Different Types of Glass Processing and Glass Finishing?
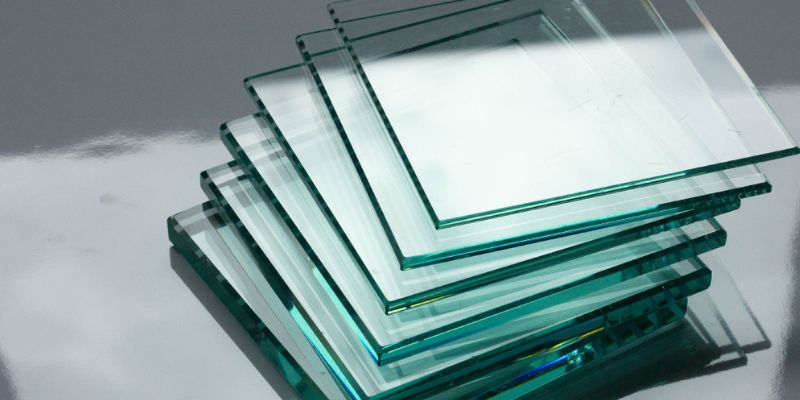
Glass processing and glass finishing is an indispensable part of the modern industry. It has played a key role in all kinds of things, ranging from architectural, automobile, and consumer electronics products to technology and optics. With the advancement of technology and techniques, glass processing and glass finishing and manufacturing are constantly upgrading, bringing different prospects to various fields. In this article, we will further discuss glass processing and glass finishing technology and applications and understand their impact on various industries so that you can be fully aware of the details of glass processing and glass finishing!
What is Glass processing and Glass Finishing?
Glass processing and glass finishing is the process of transforming glass materials into products with specific functions, shapes and characteristics through a series of processing techniques and technologies, and being suitable for different purposes and necessities. Glass processing and glass finishing broadly includes cutting, grinding, sanding, drilling, heat treatment, bending, coating, bonding, polishing, etc. More specifically, coating, bonding, and polishing are glass finishing techniques. Glass processing and glass finishing has a wide range of applications, covering many fields such as architecture, decoration, furniture, technology, medical care, automobile, aviation, optics, etc. New application possibilities are constantly expanding as technology advances, creating various special, practical and innovative products.
Common Glass Processing Methods
CNC Special Shaped Grinding
CNC Special Shaped Grinding is applied in cutting, grinding, and drilling works through high-precision digital control system. This technique supports a variety of cutting paths. In addition to round, diagonal, and special shaped cuts, it can also be applied in precision hole reaming, accurate hole position machining, edge grinding with the use of CCD positioning system. Moreover, it can correct the actual grinding size to achieve ±0.02mm grinding accuracy, ensuring high-precision glass processing quality and tolerance standards, providing customized services to meet specific requirements.
Physical Tempering
The purpose of physical tempering is to enhance the impact resistance and strength of the glass, as well as improve the durability and safety of the glass products. The processing method is based on a controlled heating and rapid cooling process, which creates compressive stress on the glass surface and increases the overall strength and abrasion resistance. Physical tempered glass is mostly used in products that need to resist harmful light rays such as ultraviolet radiation, infrared radiation, and lasers, as well as withstand heat, cold, and impacts.
Chemical Tempering
Chemical tempering is performed by ion exchange to form a stress layer on the surface of the glass, where sodium ions will be replaced by potassium ions to achieve high load-bearing capacity, strengthening, impact resistance, and pressure resistance. Chemically tempered glass is more than five times stronger than ordinary glass and is mostly used in applications that require resistance to extremely high and low temperatures, protection against dust and water, or mechanical equipment for exploration.
Edge Grinding
Edge grinding is a more common glass processing technique, which aims to grind the edges of cut glass, eliminate jagged or uneven edges, making them smooth and safe, while reducing the risk of being cut. In addition to smooth edge grinding, different grinding tools can also be used to grind the edge into beveled, rounded, and flat matte edges to ensure the glass edges meet the high-quality requirements.
Cutting
Cutting can be done in straight or curved lines with shapes such as squares, circles, trapezoids, triangles, sectors, and irregular polygons. Large machines are mostly used for cutting glass for everyday life and buildings with shapes of squares, rectangles or circles. However, diamond cutting tools are required for special needs, such as glass substrates for touch panels, semiconductors and solar panels, in order to achieve precise cutting results. Different types of cutting tools may be used to cut different thicknesses, specifications, and shapes of glass to ensure crucial cutting precision and quality. Edge grinding should be performed after cutting to achieve smooth and safe edges.
Drilling
Glass drilled processing is applicable to all kinds of optical glass, including architectural, household or industrial glass, etc. The common holes are 1mm to 40mm round holes. Square or polygonal holes may also be drilled in special cases. When drilling holes, it is necessary to determine the location of the holes before using professional equipment and drills to apply pressure along with high-speed rotation and ensure the accuracy of hole location. Grinding should be applied after drilling to smooth the edges of the holes.
Common Glass Finishing Methods
Polishing
Polishing is a finishing technique that can enhance the appearance of glass and dirt-resistant. For example, automobile glass will be polished before coating so that the adhesion between the coating layer and the glass surface is stronger, making the coating last longer. In the case of optical glass, depending on different special uses, such as observation and anti-reflection, it requires stable optical properties. Hence, it requires high manufacturing specifications and a higher degree of precision to avoid minor defects that could affect performance. These glass surfaces must remain shiny and smooth.
Bonding
Bonded is a glass finishing technique to bond two or more glass sheets, or glass and other materials together. It is commonly applied to make insulated glass, laminated glass, and bonded optical glass, etc. Larger pieces of glass are usually bonded by specialized gluing equipment, while the optical glass is bonded with optical adhesive. In addition to bonding, optical adhesive has other advantages, such as weather-resistant, corrosion-resistant, high transmittance, glare-reducing, and smoothing out minor unevenness.
Coating
Coating is applied to produce different effects through the differences in the thickness of coating layers and the film interface refractive indexes. This glass finishing technique is mostly applied in architectural, automobile, electronic and optical projects. In addition to protecting glass surfaces from being scratched, coating may be applied to change colors, reflectance, transmittance, scattering, and thermal insulation. Common types of coating include: anti-reflective coating, anti-glare coating, anti-fingerprint coating, metal coating, short wavelength pass filter, long wavelength pass filter, etc.
〈Extended reading:What is the Principle of Optical Coatings?〉
Practical Applications in Glass Processing and Glass Finishing
Construction Industry
Glass processing and glass finishing is used in the construction industry for applications such as windows, doors, curtain walls and roofs. It is basically utilized for cutting and grinding. For decorative arts, etching and coloring may also be applied to create other effects. Most of the glass used on the exterior of buildings is coated with a film. Coating affects transmission of light and solar heat energy, as well as the comfort in buildings, the efficiency of the ventilation and air-conditioning systems, and the color and reflection of the glass surface. The latest technology in architectural glass is Low-E glass (low emissivity glass). Its surface is coated with multi-layer metal, or film layers composed of compounds with high light transmittance, shock resistance, and high mid-far infrared reflection.
Automobile Industry
The windshield of an automobile is arguably the part of the car that requires the most efforts to conduct glass finishing. Glass coating can prevent the glass surface from being scratched directly, and can also resist corrosion, heavy rain and reflected light, impact and high temperature. The more layers of coating, the stronger the protection is. Optical coating technology is also applied in car accessories such as car panels, car camera lenses and head-up displays.
General Livelihood Products
There are many products in our lives that utilize glass, including furniture, utensils, decorations, and the exterior of electrical appliances. Glass cutting and grinding processing techniques are more commonly used in the manufacturing process. If special effects are required, sandblasting, embossing, engraving and other techniques may be applied. However, the processing steps and methods will be simpler than other application fields.
Optical Products
There are a wide range of optical products, such as consumer electronics camera lenses, monocular camera lenses, optical fibers, photocopiers, cameras, microscopes, scanners, and optical mice, etc. There are many electronic and non-electronic products requiring glass processing in our daily life where optical coating techniques are applied to help reduce reflection and glare and the appearance of fingerprints while improving visibility and light transmittance or lighting effects. Different coating methods for glass can create different light transmission features.
Piezoelectric Products
Piezoelectric products are usually made of synthetic quartz glass, which can be made into various shapes and thicknesses. The principle of glass processing is that the material polarizes under pressure, resulting in a product with high strength, shock resistance, high force-electricity conversion sensitivity, and easy matching with acoustic impedance. Hence, these products are suitable for use in aerospace and mobile base station related equipment, such as vibration sensors, transducers and control systems.
Planar Optical Splitters
Planar optical splitters are composed of thin and flat coated glass panels. They are commonly made by quartz, D263T, Corning EXG, BF33, and H-K9L. Their main function is to split a beam into two beams. Most planar optical splitters are coated with a beam splitter film on one side and an AR antireflective film on the other side to increase transmission and reduce ghosting. It has a wide range of applications in microscopes, imaging systems, optical fiber communication systems, laser manufacturing and test instruments.
Conclusion
Since glass has been widely applied, glass processing and glass finishing is always in demand. With different processing and finishing methods, changes may be made to the functions, appearances, performances of glass in order to be applied in various industries. YANG EN TECH CO., LTD. is a professional optical coating OEM and ODM with over 15 years of optical class processing experiences. We provide glass processing and optical coating services. We also offer specifications, as well as precision processing services, tailored to customers’ particular needs, covering a wide range of applications, including 3C technology, automobiles, aerospace industries, etc. to help customers reduce errors in glass processing and maintain product quality. Please contact us if you have any requirements.