- Home
- Blog
- Optical Coating
- Understanding PVD Coating: Enhancing Surface Performance.
Understanding PVD Coating: Enhancing Surface Performance.
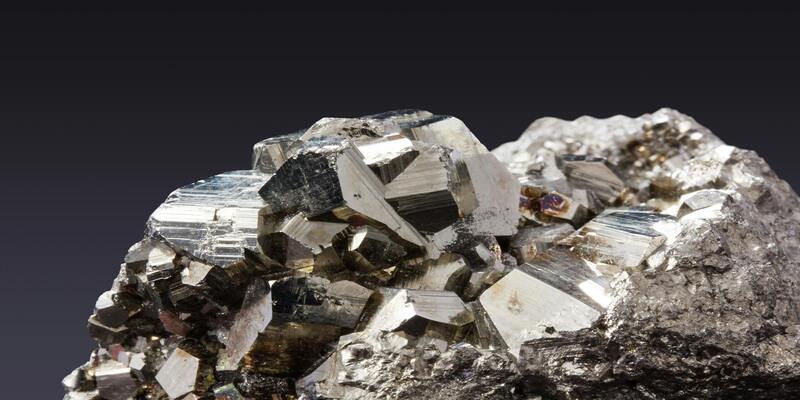
What is PVD Coatings?
In the field of optical coatings, PVD (Physical Vapor Deposition) technology is commonly used to form various types of thin films. PVD technology, applied in optical coating, can form thin film layers on the surface of different substrates, thereby improving the related optical performance, surface characteristics, and durability. Moreover, PVD technology possess high purity, uniformity, and consistency, effectively enhancing the optical
performance and reliability of products.
〈Read More:What is the Principle of Optical Coatings?〉
What are the advantages of PVD coatings?
Compared to CVD (Chemical Vapor Deposition) technology , PVD (Physical Vapor Deposition) technology has the following advantages:
1. High purity: Generally speaking, PVD technology has high purity because films are formed through physical vapor deposition, without the need for solutions or chemical reactions.
2. High controllability:PVD technology offers superior controllability, allowing precise control over the thickness and structures of the films. Additionally, it exhibits high consistency, which contributes to excellent durability.
3. Wide application:PVD film layer technology can be applied to various materials, with targets including metals, oxides, nitrides, and so on, making it suitable for producing different types of optical films. In contrast, during CVD process, gas-phase reactions are involved, requiring the selected materials to have appropriate gas-phase reactivity to undergo chemical reactions and form film layers.
4. Environmentally Friendly:During PVD process, no chemical substances are required. In contrast, during CVD process, chemical gases are typically used as reactants, posing potential environmental and operational safety risks.
To sum up, PVD technology does not involve chemical reactions and does not require a specialized gas supply system. The optical films are highly controllable and consistent, and have a wide range of applications. PVD technology can provide high-quality optical coatings and meet the needs of different fields.
〈Read More:What are Filters? Let’s Learn about 7 Common Filters and Their Applications!〉
The main types of PVD Coatings
The main types of PVD inclide vacuum evaporation, sputter deposition, cathodic arc deposition, electron beam deposition, and pulsed electron deposition. These techniques are widely applied from electronics manufacturing to industrial processing. Further details will be provided below.Vacuum deposition
Vacuum Deposition is an optical film coating technique whereby materials are heated to evaporate and then deposited onto a substrate surface. In this process, materials such as metals or metal oxides (oxides, sulfides, etc.) are heated to high temperatures in a vacuum environment, causing them to melt and evaporate. The evaporated material particles (atoms/molecules) adhere to the surface of the substrate, forming a thin film, while the thickness and structure of the film layer can be adjusted accordingly.
Sputter deposition
Sputter Deposition is an optical film coating technique in which a target material and an ion source are set up in a vacuum chamber. The target material is bombarded by an electric arc or plasma generated by the ion source, and then deposited onto a substrate to form a thin film. Sputter deposition technology can produce uniform thin films over large areas, and the sputtered atoms have relatively high energy, resulting in good adhesion of the film layers.
Cathodic arc deposition
Cathodic Arc Deposition is an optical film coating technique conducted by placing a target material and a cathode in a vacuum chamber. This method involves bombarding the target material with high-energy cathodic arcs, which then deposit onto the substrate surface to form a thin film. Cathodic Arc Deposition technology boasts high deposition rates, making it more efficient for mass production, thereby enhancing production efficiency and shortening production cycles.
Electron beam evaporation
Electron Beam Deposition is an optical coating technique performed in a vacuum chamber, where an electron beam is focused to bombard the target material, heating the target material to its evaporation temperature, and then depositing it onto the substrate surface. Due to the high power density of the electron beam, it can evaporate high melting point metals or sublimate materials, and the electron beam can be precisely controlled through electric and magnetic fields.
Pulsed electron deposition
Pulsed Electron Deposition is an optical coating technique which involves using high-power pulsed lasers in a vacuum chamber to bombard the target material, causing the target material to evaporate and deposit onto the substrate surface to form a coating film. The most significant feature of pulsed electron deposition technology is that the elemental composition ratio of the coating film remains nearly the same as that of the target material, making it particularly suitable for applications requiring high-purity coatings.
How are PVD Coatings applied?
PVD technology have been widely applied in various fields, such as:
1. Optics: To manufacture optical components such as metallic mirror coatings and filters to enhance optical performance and durability.
2. Electronics industry:To be utilized in the production of semiconductor devices, displays, solar cells, and so on. A variety of target materials are available to meet various needs and improve its optical performance and corrosion resistance.
3. Automotive Industry:To be used in automotive applications such as car window glass, car body coatings, headlights, wheel covers, etc., to enhance wear resistance, corrosion resistance, and aesthetics in related desings.
4.Medical Devices: To be used for coating implants to improve biocompatibility and durability.
In addition, PVD technology is also applied in kitchenware, home decor, bathroom fixtures, personal jewelry/accessories, etc., with a very wide range of applications in daily life. It can enhance the quality, durability, and aesthetics of various products, providing users with a better product experience.
〈Read More:What is AR (Anti-Reflection) coating? 〉
〈Read More:Beamsplitters Guide: Principles, Types, and Applications〉
Our company currently holds utility patents for innovative optical sensing device structures: the black film structure and the metal film structure. The black film structure is achieved through PVD technology, where chromium (Cr) is deposited onto the substrate surface to maintain a stable reflectance for optical sensing devices. On the other hand, the metal film structure involves depositing silver (Ag) onto the substrate surface using PVD technology, generating a larger quantity of refracted light for optical sensing devices. This technology has already been utilized in satellite-related projects.
Material selection for PVD coatings
In the field of optical coatings, glass is the most commonly used substrate material, while PVD (Physical Vapor Deposition) technology utilizes a variety of target materials. Common optical coating target materials include metals and oxides; the types and characteristics are as follows:
1. Metal Targets:Metal targets are used to form metal thin films, such as aluminum (Al), silver (Ag), chromium (Cr), nickel (Ni), titanium (Ti), etc. Metal thin films are commonly used in optical components for metallic reflector mirrors, providing high reflectivity. Additionally, the typically smooth and flat surface of metal-coated films helps maintain optical consistency.
〈Related Patents:Black Chrome Coating for Optical Sensor Unit, Metallic Silver Coating for Optical Sensor Unit〉
2. Oxide Targets:Oxide targets are used to form oxide thin films, such as titanium dioxide (TiO2), silicon dioxide (SiO2), tantalum pentoxide (Ta2O5), etc. These films are commonly employed in optical devices for anti-reflection coatings, filters, dielectric mirrors, etc. Among them, tantalum pentoxide (Ta2O5) has been widely applied in semiconductor components in recent years due to its excellent optical performance and chemical stability.
The selection of target materials significantly impacts the transmittance/reflection of filters. Therefore, choosing the appropriate target materials allows for the modulation of optical properties, making them better suited to specific application requirements.
〈Read More:What is anti-glare (AG)? 〉
Conclusion
YANG EN TECH CO., LTD. have over 15 years of experience in providing services including optical coating designs, optical filter manufacturing, glass processing/finishing, and all kinds of optical coatings. Should you have any requests for optical coatings, please do not hesitate to Contact us!